Electrostatic Precipitation (ESP) - Wet ESP
Wet ESP Service & Technical Information
How It Works
The PPC Industries Wet electrostatic precipitator (WESP) is used for particulate control, opacity control, and MACT Compliance. The WESP can operate either downflow, or upflow depending upon the gas stream characteristics. Pre or post treatment scrubbers can be incorporated into the design to accomplish acid neutralization or VOC removal.
The design to the left illustrates a down flow WESP. Gas enters the roof of the electrostatic precipitator where perforated plates and turning vanes evenly distribute the gas before entering the collection tubes. The collection tubes are bundled in a honeycomb arrangement to provide the necessary particle residence time, velocity, and collection plate area. Two sets of spray headers are installed above the collection tubes. The first spray header provides a fine mist where the water droplets become immediately charged and flow down the sidewall of the collection tube, co-current with the gas flow. This continually wets the tubes to prevent sticky particulate from adhering to the tubes during the collection process. The second spray header is a flushing system which periodically sprays a larger amount of water to flush the collected precipitate out of the collection tubes and into the lower plenum. The misting and flushing occur simultaneously with the particulate collection process. Particulate control is accomplished by charging the particles, collecting the precipitate on the tubes which operate at ground potential while simultaneously misting and flushing.
Centered in each collection tube is a rigid electrode with corona generating pins. Each electrode is suspended from an adjustable support rack. The support rack is suspended from high voltage insulators located out of the gas flow. The insulators are blanketed with a continuous flow of heated purge air. A 65 to 80 KV transformer rectifier energizes the electrode rack using an automatic T/R controller.
As the dust and condensed aerosol particles enter the wet electrostatic precipitator collection tubes, they become charged from a bombardment of negatively charged electrons. The negatively charged particles adhere to the wetted collection tubes and are periodically flushed into the lower plenum of the electrostatic precipitator (ESP).
The lower plenum is designed to demist the gas and drain the collected precipitate out of the particulate control equipment. Ancillary water treatment can be incorporated into the design. Each PPC air quality control system including the wet electrostatic precipitator (WESP), the dry electrostatic precipitator (ESP), the biofilter, SCR, and the dry acid gas scrubbing system is designed to meet the customer objectives for EPA and corresponding MACT Compliance.
PPC has completed over 500 successful air pollution & particulate control projects, and with over 40 years of experience PPC has been a stable force in the field of electrostatic precipitation.
Have questions about Electrostatic Precipitation (ESP) - Dry ESP?
Ask a PPC Industries ExpertInstallations
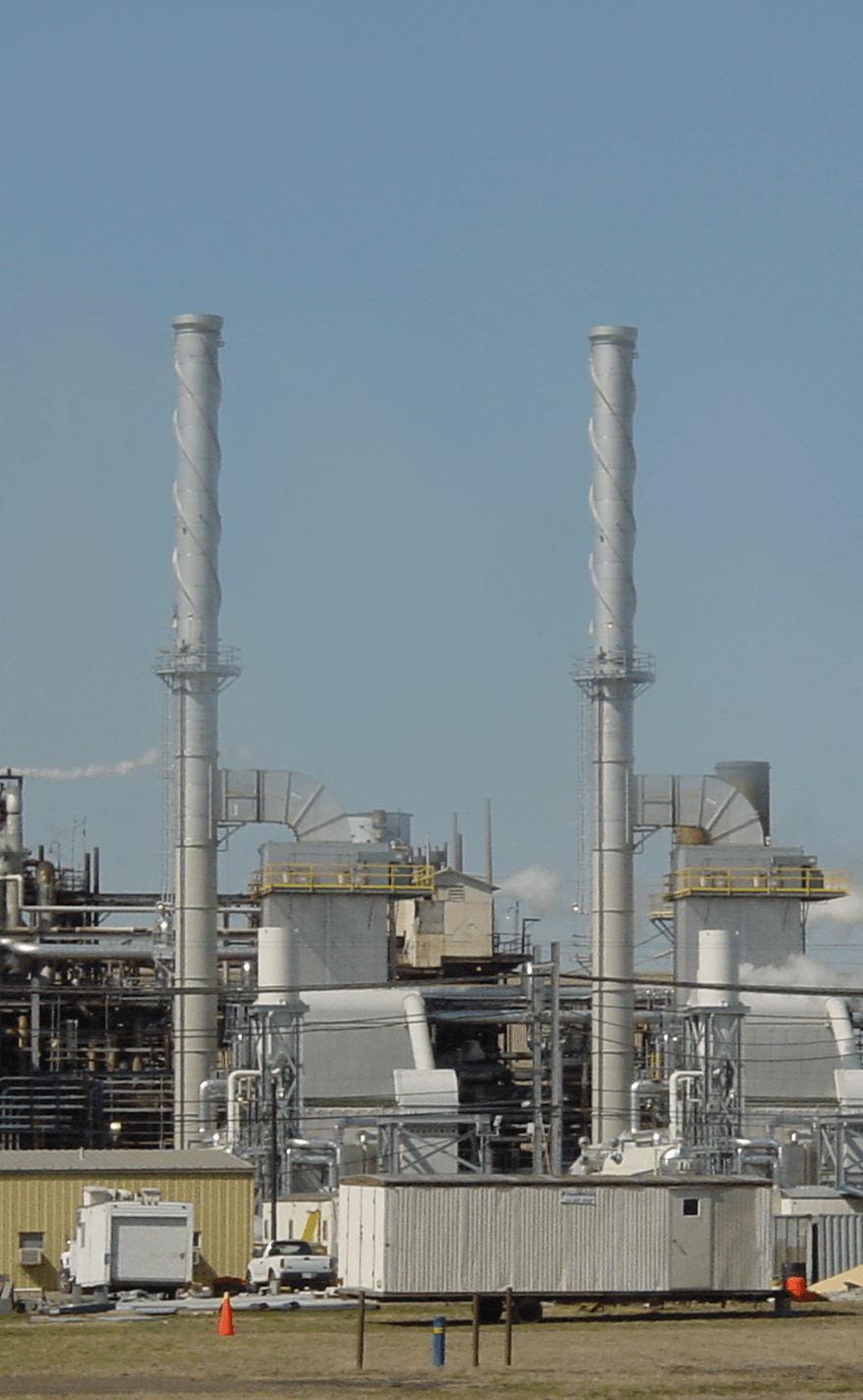
360,000 ACFM - Refinery Boiler Emissions:
- Application: Refinery Boiler Flue Gas Emissions
- Industry: Refining
- Location: New Jersey
- Air Flow: 360,000 ACFM
- Pollutants: Sulfuric Acid Mist, Ammonium Bisulfate, Mineral Ash
- Objective: Particulate Compliance
- Notes: Four independent 90,000 acfm systems with cooling towers
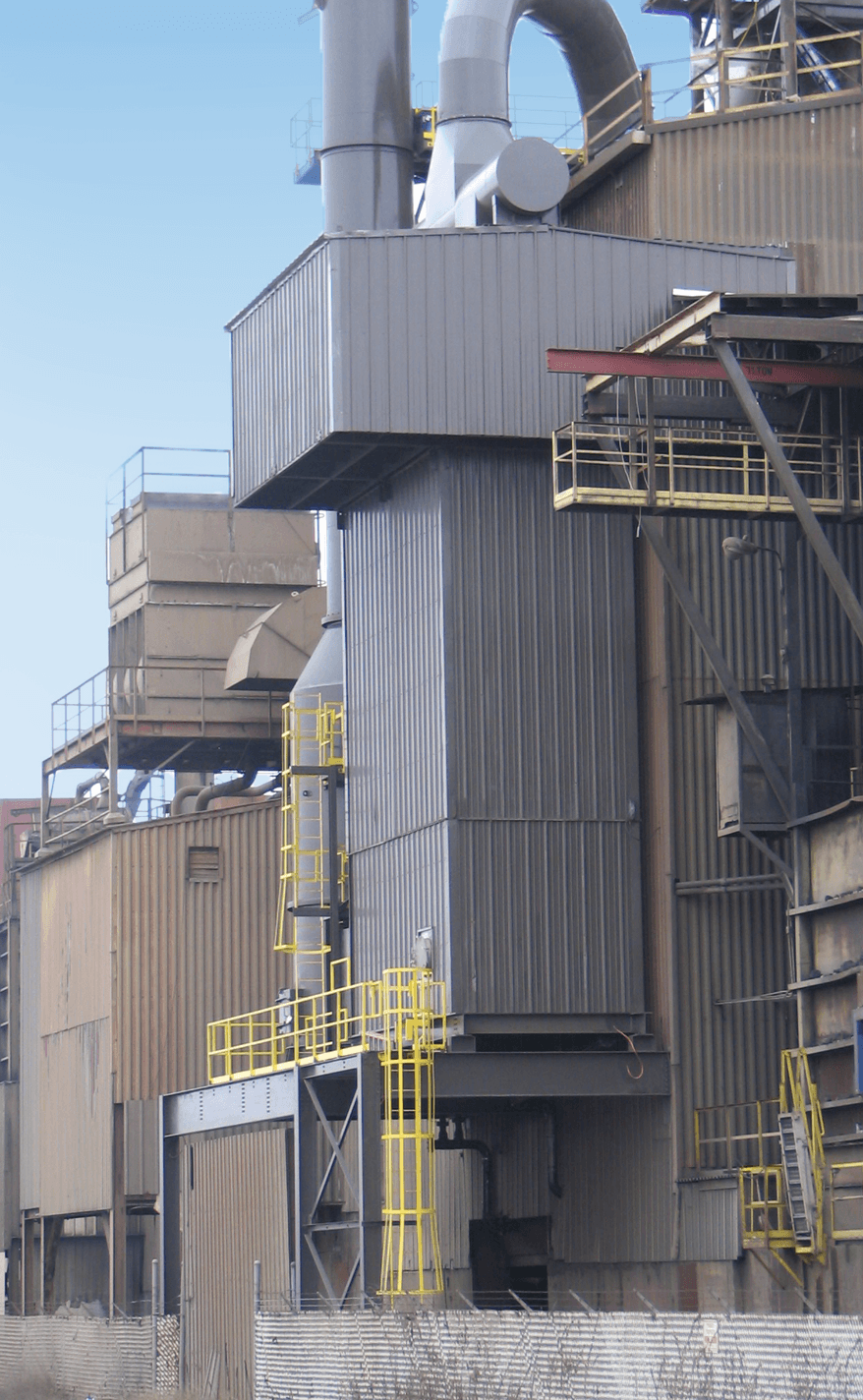
67,000 ACFM - Iron Cupola
- Application: Iron Cupola
- Industry: Foundry
- Location: Indiana
- Air Flow: 67,000 ACFM
- Pollutants: Lead, Mercury, Beryllium
- Objective: PM
- Notes: N/A
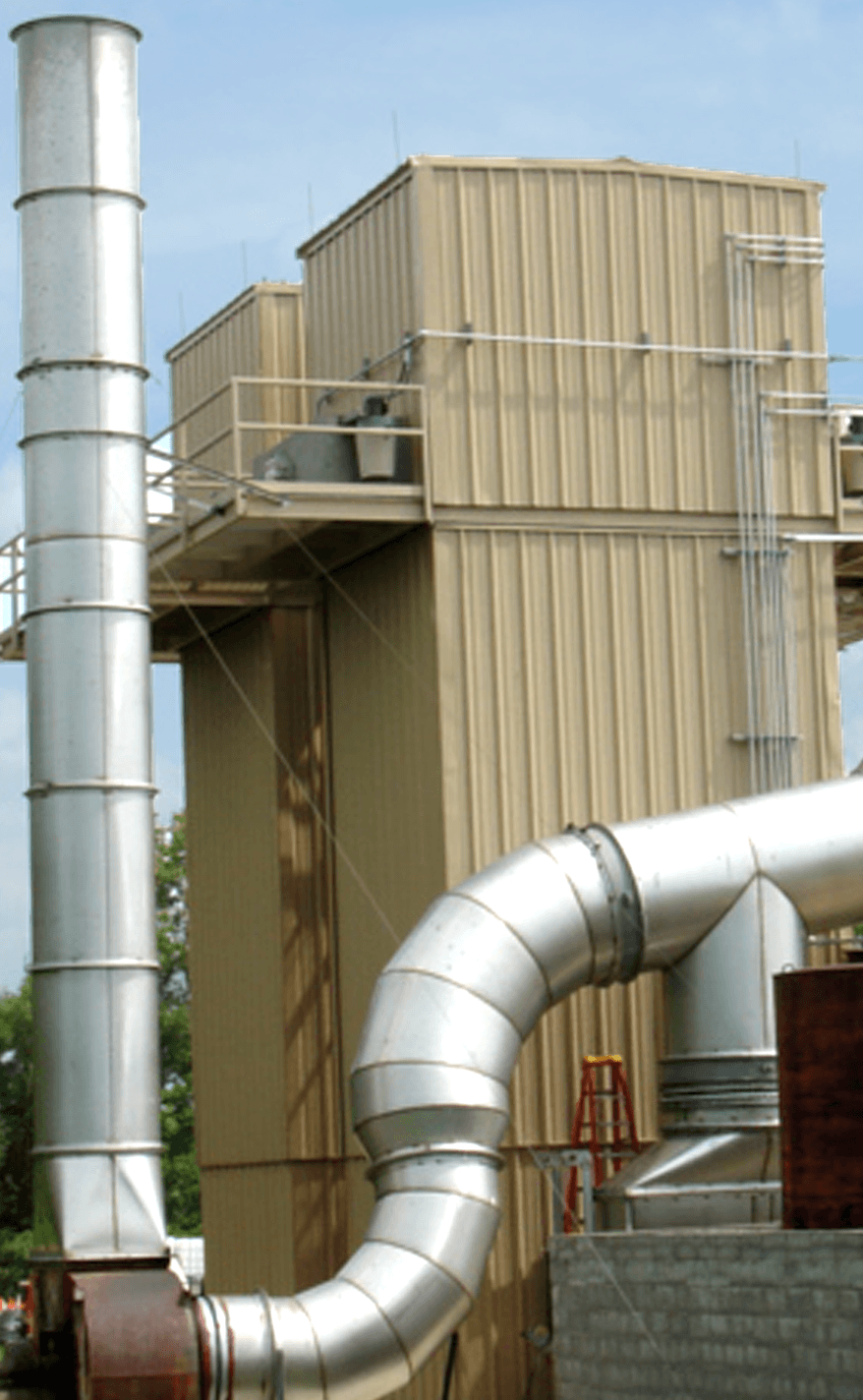
50,000 ACFM - PVC Ovens
- Application:
- Industry: Highway Safety Cones
- Location: Chicago, Illinois
- Air Flow: 50,000 ACFM
- Pollutants: Proprietary Information
- Objective: Opacity
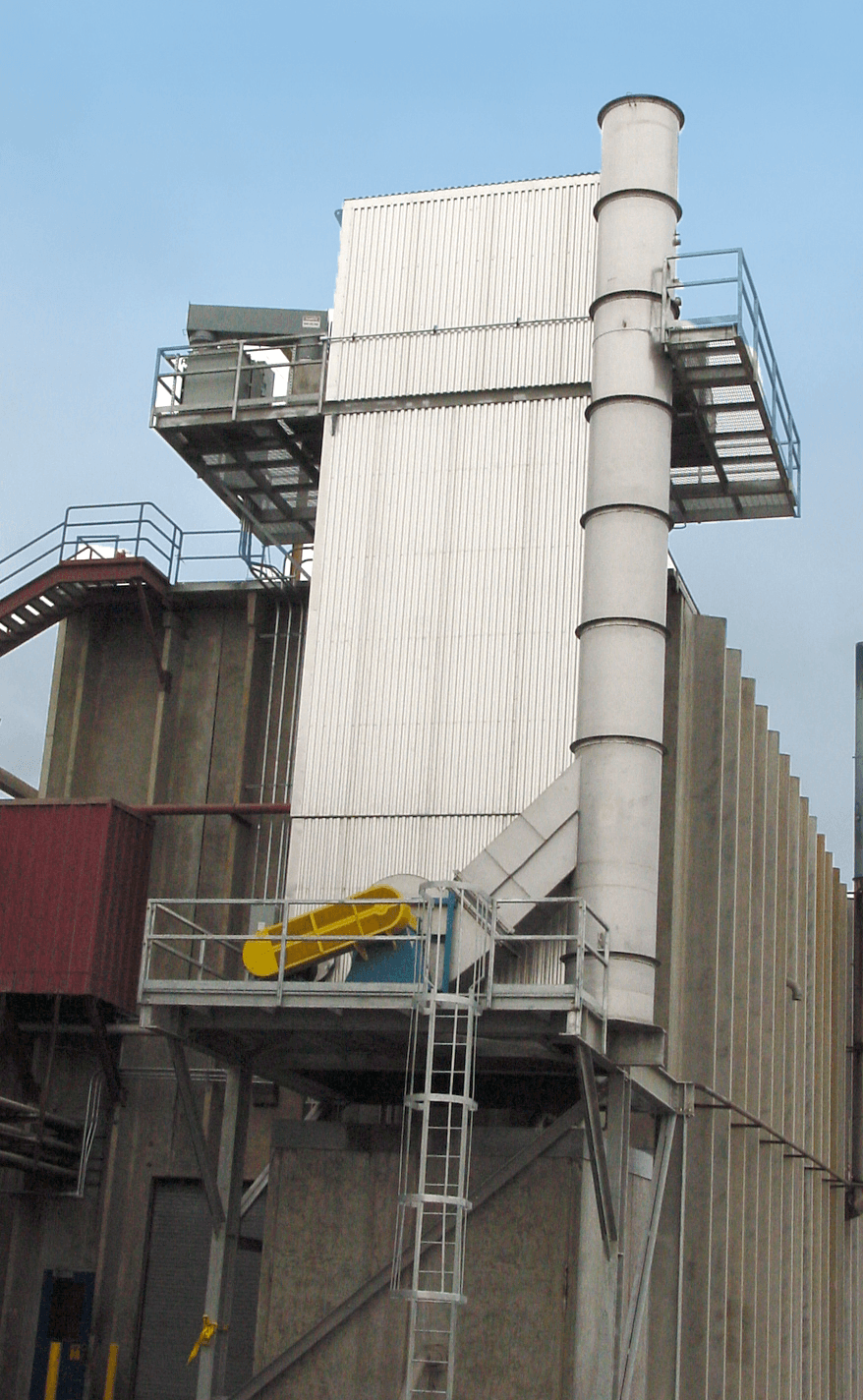
35,000 ACFM - Fryer Exhaust
- Application: Treatment of Fryer Vent Exhaust
- Industry: Food Processing
- Location: Washington
- Air Flow: 35,000 ACFM
- Pollutants: Condensable Oils, Fats and Greases
- Objective: Particulate & Opacity Compliance
- Notes: Complete turnkey installation included duct, structural, foundation and electrical as well as the WESP
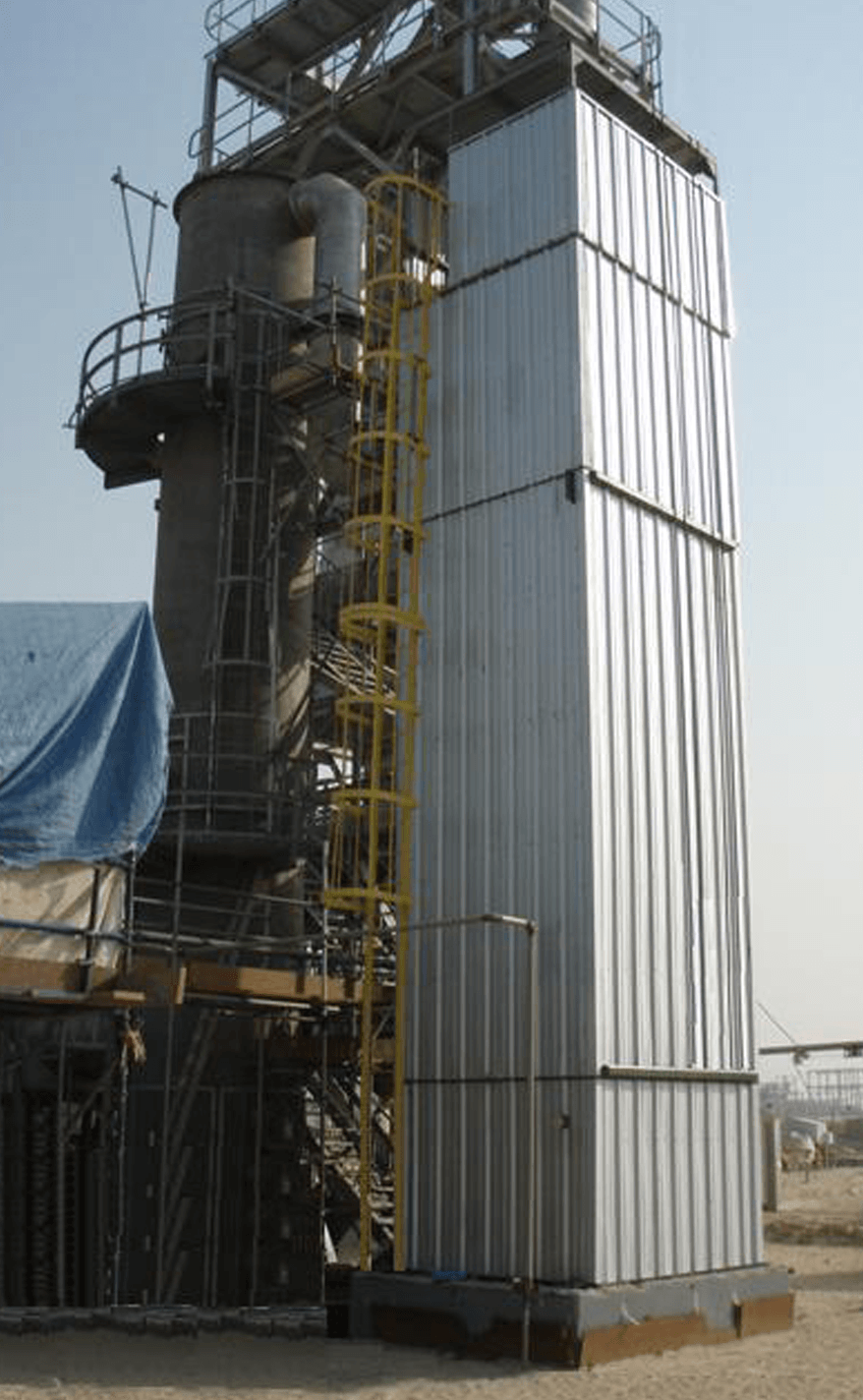
14,000 ACFM - Glycol Incineration
- Industry: Glycol Incineration
- Location: Saudi Arabia
- Air Flow: 14,000 ACFM
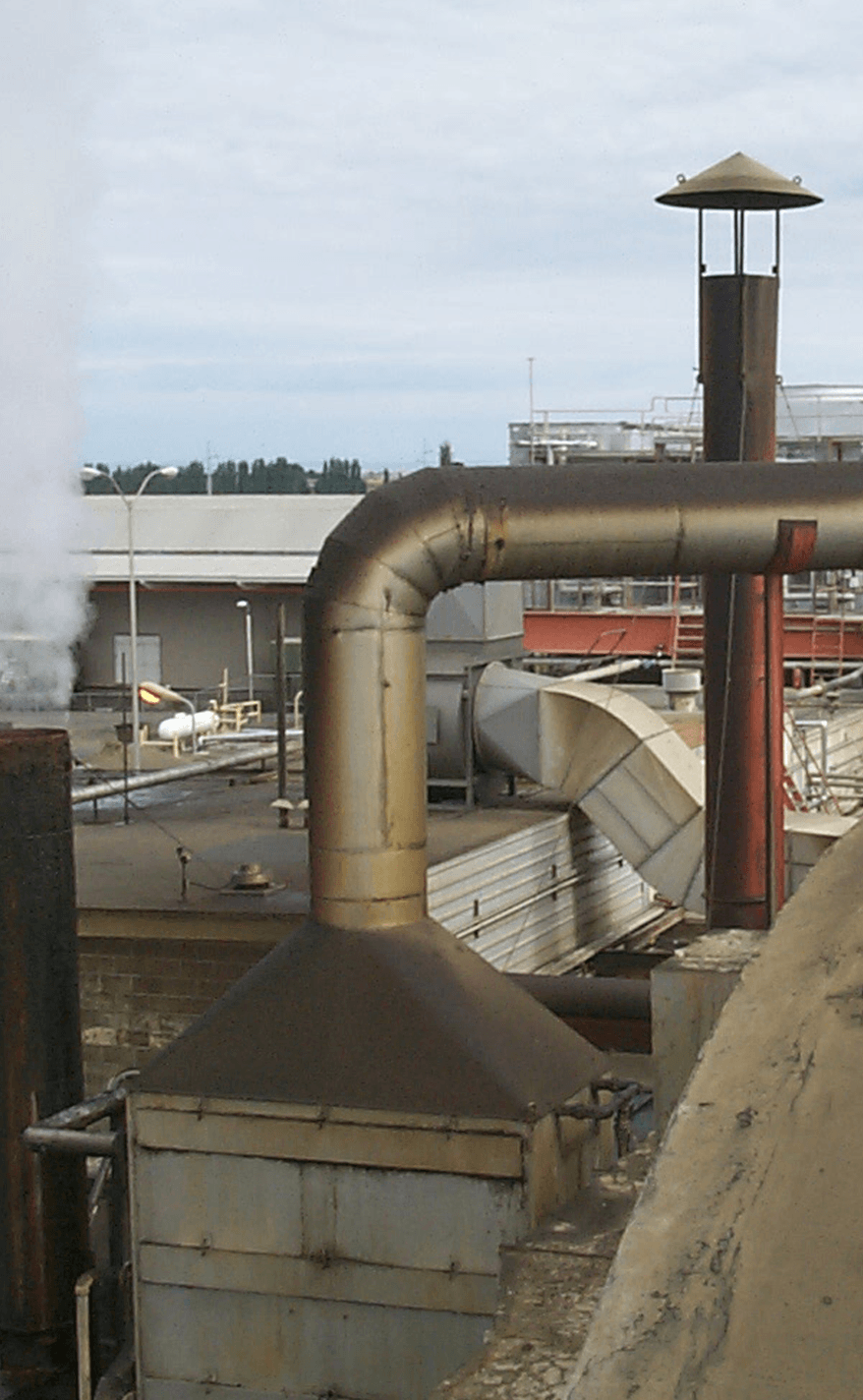
20,000 ACFM - Fryer Exhaust
- Application: Treatment of Fryer Vent Exhaust
- Industry: Food Processing
- Location: Washington
- Air Flow: 20,000 ACFM
- Pollutants: Condensable Oils, Fats and Greases
- Objective: Particulate & Opacity Compliance
- Notes: Prefabricated unit only took five days to install